How to Choose the Best Welding Systems For Your Business
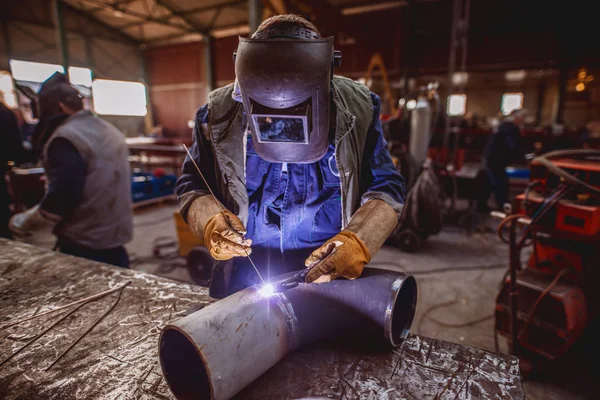
Choosing the right welding system for your business is like finding the perfect pair of shoes. It needs to fit just right, be reliable, and meet all your specific needs. Whether you’re new to welding or a seasoned pro, selecting the best welding system can feel overwhelming with the myriad of options out there. But don’t worry! Let’s break it down together and make this decision a breeze.
Understand Your Welding Needs
First things first, you need to identify what you need the welding system for. Are you working with thin metals, thick steel, or perhaps a variety of materials? Different projects require different welding techniques, so understanding your primary use case is crucial.
Types of Welding
Let’s explore the four main types of welding, and check out ISAT to see some of the best systems available.
MIG Welding (Metal Inert Gas)
MIG welding is often the go-to for beginners. It’s ideal for thin metals and home projects, offering a quick and relatively easy learning curve.
TIG Welding (Tungsten Inert Gas)
If you need high precision and clean welds, TIG welding is your best bet. It’s suitable for a wide range of metals, including aluminum and stainless steel, but requires more skill and patience.
Stick Welding (Shielded Metal Arc Welding)
Stick welding is highly versatile and works well in outdoor conditions. It’s great for thicker materials and heavy-duty projects, requiring some skill but known for its robustness and dependability.
Flux-Cored Arc Welding (FCAW)
Similar to MIG welding, FCAW is better suited for thicker materials and can be used outdoors, even in windy conditions. It produces strong welds quickly.
Each of these welding types has its strengths and is suited to different kinds of work. Understanding these differences is the first step to making an informed decision.
Assess Your Work Environment
Your work environment plays a significant role in choosing a welding system. Are you welding indoors in a controlled environment, or are you working outdoors where conditions can vary? Here’s why this matters:
Indoor vs. Outdoor Welding
Indoor Welding
When welding indoors, there’s less concern about wind or weather affecting the weld. Options like MIG and TIG are often preferred for their precision and control.
Outdoor Welding
Wind can affect the shielding gases used in MIG and TIG welding, making Stick and FCAW better choices. Durability and portability of the equipment are crucial in these settings.
Power Requirements
Welding machines come with different power requirements. Make sure to match the welding system to your available power supply. Here are some key points to consider:
110V vs. 220V Power Supply
A 110V power supply is suitable for light to medium welding tasks and can be plugged into standard outlets. For heavier tasks and industrial work, a 220V power supply is necessary, which requires a specialized outlet.
Single Phase vs. Three Phase
Single phase power is common in residential areas and is fine for small to medium tasks. Three phase power, typically found in industrial settings, provides more power for heavy-duty welding.
Budget and Cost Considerations
Budget is always a critical factor. Welding systems can range from a few hundred dollars to several thousand. Here’s a breakdown to help you think through the financial aspect:
Initial Cost vs. Long-Term Investment
A basic MIG or Stick welder can be affordable and perfect for beginners or small businesses. On the other hand, TIG welders and more advanced systems will cost more upfront. Investing in a more expensive, high-quality machine can save money in the long run through durability and fewer repairs. Also, consider the cost of consumables like electrodes, gas, and maintenance when budgeting.
Ease of Use and Skill Level
Your experience and skill level should guide your choice. While it’s tempting to go for the most advanced system, it’s essential to be realistic about what you can handle.
Beginner-Friendly vs. Advanced Systems
MIG welding systems are generally easier to learn and use, making them beginner-friendly. Stick welding, while requiring some skill, is robust and straightforward. On the other hand, TIG welding offers the highest precision but requires significant skill and practice. FCAW is powerful but may need a bit more understanding of welding principles.
Portability
Do you need to move your welding system around frequently, or will it stay in one place? Portability can be a crucial factor depending on your work requirements.
Portable Systems
Lightweight, compact models are available for MIG and Stick welding, ideal for contractors or jobs requiring movement between sites.
Stationary Systems
Heavy-duty TIG and multi-process machines are typically stationary, best suited for a dedicated workshop or factory setting.
Safety Features
Safety should never be an afterthought. Ensure your welding system comes equipped with essential safety features to protect you and your workers.
Key Safety Features to Look For
Look for thermal overload protection, which prevents overheating by automatically shutting down the machine. Voltage control ensures consistent performance and reduces the risk of electric shock. Protective housing shields internal components from dust, debris, and impact.
Manufacturer and Warranty
Choosing a reputable manufacturer with a solid warranty can save you headaches down the road. Do some research on brands and their customer support. A good warranty and reliable customer service can make a significant difference.
Reputable Brands
Lincoln Electric, Miller Electric, ESAB, and Hobart are known for their reliable welding systems.
Warranty and Support
Look for warranties that cover at least three years. Ensure the manufacturer offers robust customer support and easy access to replacement parts.
Making the Final Decision
Now that you’ve got all the information, it’s time to make your choice. Let’s summarize the critical steps:
- Identify Your Needs: Consider the type of welding, materials, and project scope.
- Consider the Environment: Think about whether you’re welding indoors or outdoors, and check your power supply.
- Set a Budget: Balance the initial cost with the long-term investment.
- Match to Skill Level: Choose a system that matches your expertise.
- Factor in Portability: Determine if you need a mobile or stationary system.
- Prioritize Safety: Ensure the system has essential safety features.
- Choose a Reputable Brand: Look for good warranties and customer support.
By taking the time to consider each of these factors, you’ll be well on your way to choosing the best welding system for your business.